Finance
US has a shortage of manufacturing workers and it threatens global competitiveness
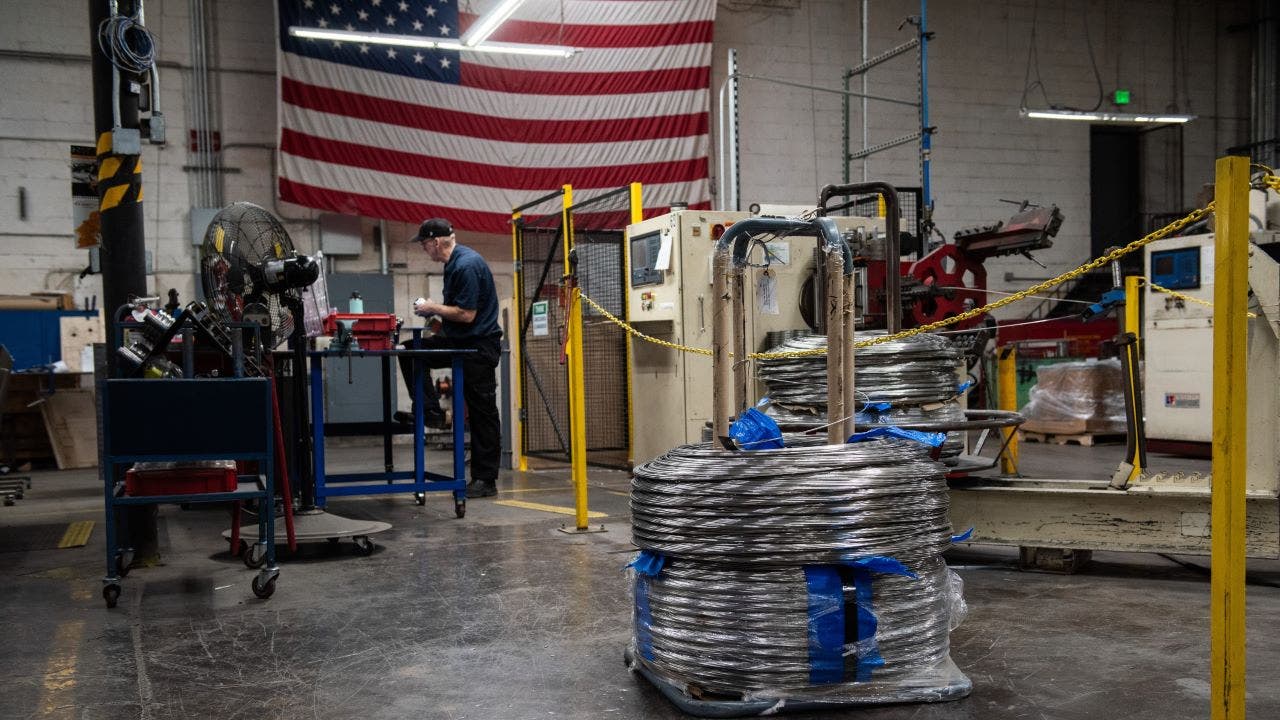
The U.S. manufacturing sector faces a widening jobs gap over the next decade as it looks to sustain the growth it has experienced in the wake of the COVID pandemic, but as many as half could go unfilled, according to a new study.
The report by Deloitte and the Manufacturing Institute (MI) projects that as many as 3.8 million additional employees will be needed in the manufacturing sector between 2024 and 2033 as current workers retire or change careers and new roles in the industry are created.
As the U.S. manufacturing sector’s need for higher-skilled workers grows, the report predicts that as many as half, or 1.9 million jobs, could remain unfilled if manufacturers aren’t able to address the skills and applicant gaps. Failing to fill those jobs could dim the prospects for companies to achieve future growth plans and hurt the U.S. manufacturing industry’s global competitiveness.
“Since COVID, we have seen a real focus on onshoring, reshoring, and of course new investment,” Manufacturing Institute President and Executive Director Carolyn Lee told FOX Business in an interview. “The reasons for that are everything from supply chain lessons we learned during COVID, but also things like tax reform that really went into effect just before COVID started, and then of course the Infrastructure and Jobs Act, the Inflation Reduction Act and the CHIPS Act all really helped spur investment in manufacturing here in the U.S.”
BIDEN REGULATIONS, EXPIRED TAX INCENTIVES WEIGH ON MANUFACTURERS
The manufacturing sector currently has more than half a million job openings. The Bureau of Labor Statistics’ Job Openings and Labor Turnover Survey (JOLTS) for February showed there were 583,000 open manufacturing jobs.
That figure was down about 91,000 jobs from a year ago and 13,000 from January, but Lee said the manufacturing sector has struggled to get below half a million openings in recent years.
“We’ve been hovering around 500,000 jobs open every month for about the last six years,” she explained. “Coming out of COVID, we had 800,000 open jobs for several months in a row. It’s just that our demand is outpacing the number of people who are looking. We have very low unemployment, of course, in the country – which is a good news story. So we’ve got to figure out how do we bring in people who may be underemployed or on the sidelines, how do we bring in and tap into new talent pools?”
ONE BIDEN MANUFACTURING REGULATION COULD WIPE OUT UP TO 1 MILLION JOBS, BUSINESS LEADER SAYS
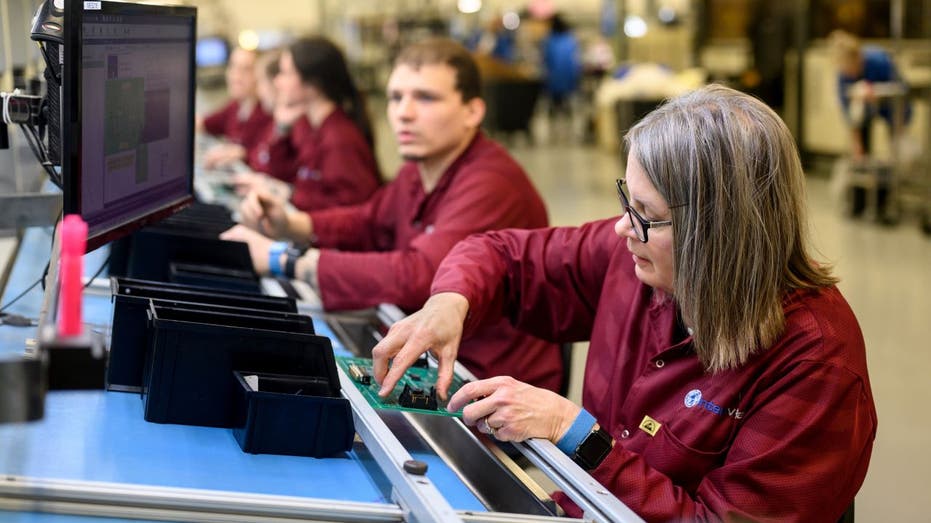
Lee noted that the new report “highlighted that highly-skilled roles like statisticians and data scientists, engineers, logisticians, computer and information systems folks as well as industrial maintenance technicians are all high demand jobs right now that we have a number of openings in and we expect to grow over this next 10 year window.”
“The thing we always highlight is that some of the open jobs are available to people with six weeks of training, and some are six or eight years of training – we have that much of a range,” she added.
Lee explained that challenges around building and retaining a skilled workforce have been the top concern for manufacturers for about five straight quarters and has been in the top three concerns for roughly eight years, according to the National Association of Manufacturers’ quarterly outlook surveys. Those workforce constraints have an impact on manufacturers’ operations.
“They’re not expanding their business, they’re not introducing new product lines, they’re not expanding their production because of the challenge they have with labor,” Lee said.
NIPPON STEEL SAYS US STEEL ACQUISITION WOULDN’T CAUSE LAYOFFS, PLANT CLOSURES
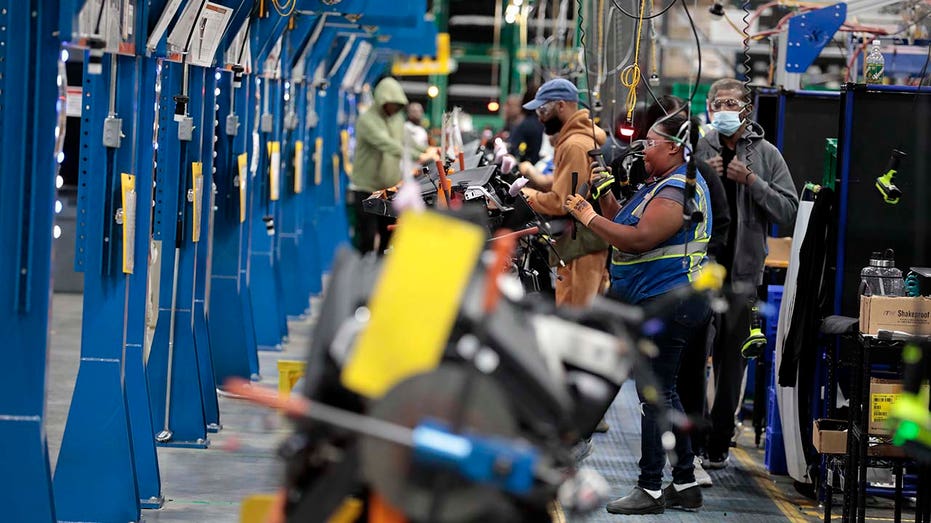
She went on to note initiatives like Heroes Make America, which helps train service members who are transitioning out of military service for manufacturing jobs, as ways to attract workers and upskill them.
The importance of training and upskilling workers was also a key finding in the report, with employees 2.7 times less likely to leave an organization if they feel like they’re getting an investment in training that can help them advance in their job.
Lee said over half of respondents indicated that flexible work arrangements are essential for manufacturing businesses to attract and retain workers. She explained that while that may not mean remote or hybrid work given the need to be in-person for production roles, flexible scheduling can be a compelling option.
“You can look at things like how do you let people switch shifts, how do you let people trade off, or build those part-time, kind of gig work roles for some of the more flexible production pieces where you can come in and just work for a few hours then pop out,” Lee explained. “There’s a lot of creativity going on in the sector.”
Read the full article here
